(And other lithium-ion battery devices)
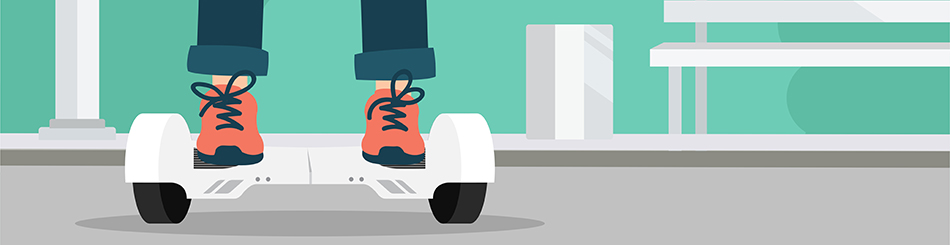
An article by K.M. Abraham (@lithiumabraham) of Northeastern University and E-KEM Sciences.
UPDATE (12/16/2016): We checked back in with Dr. Abraham to see if anything has changed since the publication of this article. According to Abraham, hoverboard manufacturers have improved the safety of the devices since wide-spread instances of explosion in 2015. This has been brought about by a certification program by the Underwriters Laboratory (UL). The UL, which is a safety consulting and certification company, has introduced their NATIONAL STANDARD UL 2272 Certification for Personal e-Mobility. Any hoverboard that is marked with the UL certification can be expected to be much safer than previous generations. Several companies, including Sharper Image, now sell UL certified hoverboards. “As with any manufactured product — and especially devices powered by very energy rich Li-ion batteries — there is a potential for safety hazard,” Abraham says. “But we can expect hoverboards to be significantly safer if UL certified.”
———————————————————————–
(Feb. 2016) Recent reports of hoverboards burning on the streets of America have created a great deal of concern about the safety of lithium-ion (Li-ion) batteries that power them(1).
This is notwithstanding the fact that that Li-ion batteries have contributed immensely to shape the modern world by being the indispensable power source of choice for portable data and voice communication devices such as smartphones, laptop computers, tablets and music players.
With very high energy densities and long discharge/charge cycle life they are the driving force behind the increasing acceptance of battery powered family cars including Tesla Model S, Nissan Leaf, Chevrolet Volt and others.
Li-ion batteries are also being developed for large scale energy storage in electric utilities, telephone and cable TV exchanges and as auxiliary power systems in airplanes such as Boeing 787 Airliners, and military fighter aircraft. The energy density of Li-ion batteries of about 300 Wh/kg or 750 Wh/l that has placed them in the enviable position of the power source of choice for wide-spread applications, from small cells to large battery packs, has also made them susceptible to safety hazards(2,3).
What’s going on?
YouTube videos of fires on conference tables, smoke and fire shooting out of cellphones and laptops, Li-ion batteries burning in the storage bins of cargo planes leading to the downing of aircrafts, smoke spewing out of the auxiliary power units in Boeing 787 airliners parked on airport tarmacs, and a large number of recent fires in hoverboards while being ridden on public roads or on charging (Figure 1), have given Li-ion batteries notoriety as a power source to be handled with utmost care and safety concern.
What is going on? It is safe to say that these well-publicized hazardous events are rooted in the uncontrolled release of the large amount of energy stored in Li-ion batteries as a result of manufacturing defects, inferior active and inactive materials used to build cells and battery packs, substandard manufacturing and quality control practices by a small fraction of cell manufacturers, and user abuses of overcharge and over-discharge, short-circuit, external thermal shocks and violent mechanical impacts. All of these mistreatments can lead Li-ion batteries to thermal runaway reactions accompanied by the release of hot combustible organic solvents which catch fire upon contact with oxygen in the atmosphere.
Safety hazards of Li-ion batteries occur when the fundamental principle of controlled release of energy on which battery technology is based is compromised by materials and manufacturing defects and operational abuses. The recent occurrence of fires and personal injuries from popular hoverboards have brought home the concerns of Li-ion battery safety while recognizing that these batteries are used uneventfully every day by billions of consumers worldwide in cellphones, tablets, music players and laptops.
Anatomy of Li-ion cells
The potential safety hazards of Li-ion batteries are understood from knowledge of the chemistry of Li-ion cells and the amount of energy stored in a commercial cell like the 18650 cylindrical cell, the building block of laptop computer power packs. A typical Li-ion cell is composed of a graphite anode (represented as C6) (negative electrode) and a lithium transition metal oxide cathode (positive electrode), usually lithium cobalt dioxide (LiCoO2) or a related layered transition metal oxide, with the two electrodes electrically separated from direct contact with each other by a 16-25 micron thick micro-porous polymer membrane separator (typically polyethylene) as depicted in Figure 2.
The porous separator allows Li-ion transport between the negative and positive electrodes through the electrolyte contained in the electrode and electrolyte pores to enable the electrochemical reaction that generates electricity from the battery cell during discharge equations [1]-[3](2). The electrolyte consists of lithium hexafluorophosphate (LiPF6) dissolved in an organic solvent mixture of the cyclic organic carbonate ethylene carbonate (EC) and one or more of solvents selected from linear carbonates dimethyl carbonate (DMC), diethyl carbonate (DEC) and ethyl methyl carbonate (EMC). Manufactures use different ratios of these solvents in the solvent mixture, along with small amounts of additive compounds, to produce electrolytes that meet the performance specifications of their batteries. The DMC, DEC and EMC are flammable liquids with low flash points of 18, 24 and 23°C, respectively. As a result, they can catch fire if the hot vapors released from the cells after a hazardous incident come in contact with oxygen present in the environment.
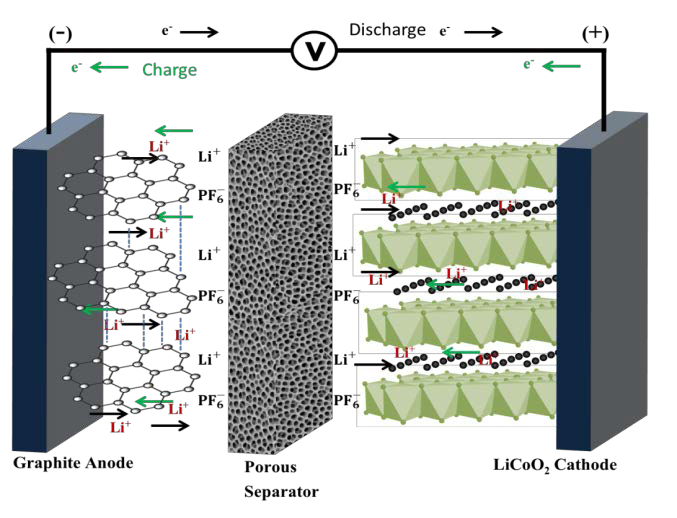
Figure 2: Schematic representation of a Li-ion cell. Fabricated in the discharged state, the cell is activated by charging during which the cathode is oxidized (see equation [1] for LiCoO2 cathode) to produce Li+ and electrons (e-). The Li+ travels through the electrolyte (composed of LiPF6 in organic solvent) and is inserted into the anode (see equation [2] for graphite anode) along with the electrons arriving at it through the external circuit. The overall cell reaction is shown in equation [3]. The opposite processes occur during discharge *(2).
Cathode: LiCoO2 Li1-nCoO2 + n Li+ + ne- [1]
Anode: C6 + n Li+ + ne- LinC6 [2]
Cell reaction: LiCoO2 + C6 LinC6 + Li1-nCoO2, Eo = ~ 4 V [3]
Commercial 18650 Li-ion cells are built with safety devices to protect them from thermal runaway reactions in case of abuse, accident or malfunction originating from manufacturing defects(3,4) (Figure 3). The safety features in 18650 cells include:
- a gas pressure release vent valve;
- a PTC (positive temperature coefficient) resistance switch device;
- and a CID (current interrupt device) as shown in the schematics in Figure 3.
The pressure release vent on the cap is set to open if the pressure in the cell exceeds a preset value determined by the manufacturer. The pressure in the cell can increase:
- if the cell experiences overcharge beyond a safe charge voltage limit, usually 4.2 V to 4.3 V;
- excessive heat from the environment in which the battery is used;
- and electrical short-circuit of the cell.
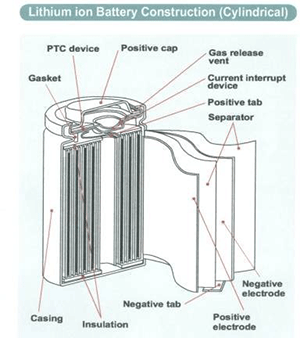
Figure 3: Schematic representation of a cylindrical 18650 Li-ion cell (See ref.4).
The PTC polymer sleeve device on the cap is a thermal switch that increases its resistance if the cell experiences a high current flow such as an external short-circuit. The increased resistance lowers the current flow from the cell and ultimately stops it if the PTC works as expected. The CID is a pressure switch that is meant to open and break the current path in the cell if the internal pressure in the cell increases as a result of heat or uncontrolled chemical reactions.
Certainly, a malfunction in the aforementioned safety devices can lead to safety hazards in an 18650 Li-ion cell. Also, it is well known to those skilled in the design, fabrication and use of Li-ion cells that the aforementioned safety devices are not always able to prevent a thermal runaway reaction, especially that ensues from an internal short- circuit, since the “inside-out” reaction in that case occurs so fast that the safety devices are not able to respond quickly to prevent them.
Why voltage and temperature matter
Generally, Li-ion cells built with the layered metal oxide cathode materials LiCoO2 (LCO), LiNi0.8Co0.2O2(NC), LiNi0.8Co0.15Al0.05O2 (NCA) and LiNi0.33Co0.33Mn0.33O2 (NCM) are susceptible to overcharge hazards while those containing LiMn2O4 and LiFePO4 are more stable during overcharge. We have studied the safety hazard of Li-ion cells containing the NC cathode and graphite anode under overcharge conditions. The data in Figure 4 display the voltage and temperature profiles of the NC cell that vented with smoke and fire upon overcharge.
When Li- ion cells with layered transition metal oxide cathodes are overcharged to 4.7 V or higher, the cell temperature increases rapidly, and the cathode becomes unstable and violently reacts with the electrolyte. The reaction produces enough heat to increase the cell’s internal pressure above the vent pressure of the burst disc, causing the cell to eject its hot internal content that catches fire and/or explodes; (see the video below depicting the violent response of a 2 Ah Li-ion cell with graphite anode and NCM cathode to overcharge. The cell was packaged in metallized plastic pouch and restrained between two polycarbonate discs during the test).
The total heat produced from a Li-ion cell in the event of short-circuit and the maximum temperature that cell will experience from this heat can be calculated, given the specific heat of the cell. The specific heat of a typical Li-ion cell has been measured experimentally to be 1 joule per degree Kelvin per gram(2). A state-of-the-art 18650 Li-ion cell with 3.2 Ah capacity and an average voltage of 3.6V produces 11.5 Wh (41400 Joules) of energy. The weight of the 18650 cell is about 46 grams.
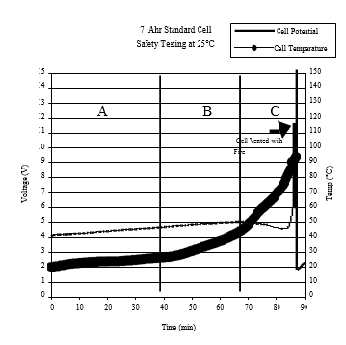
Figure 4: Voltage and cell skin temperature profiles during overcharge of a 7Ah Li-ion cell with LiNi0.8Co0.2O2 cathode and MCMB graphite anode.
We can calculate that the 41400 Joules of heat will raise the temperature of the 46 gram cell by 900 °C under adiabatic conditions if a short-circuit or another event causes a thermal runaway reaction. That means that if an 18650 Li-ion cell operating at 20 °C short-circuits its temperature under adiabatic conditions can rise as high as 920 °C. At such high temperature the graphite anode will lose its SEI stability, the polymer separator will melt, the cathode will decompose, and the Al current collector will melt and react with the electrolyte and other cell components generating additional heat.
Indeed studies have shown that the lithiated graphite (LiC6) anode begins to lose its stability and becomes very reactive towards the electrolyte beginning at around 90 °C producing heat. Furthermore, in a fully charged battery the
LiCoO2 cathode begins to decompose at about 190 °C (and the other layered metal oxides mentioned above at somewhat higher temperatures) initiating thermal runaway reactions.
Defects lead to short-circuits
The thin micro-porous polymer separator can be a point of origin of defect leading to the cell’s internal short-circuit and catastrophic failure. An internal short-circuit can arise from the breach of the very thin separator membrane that electrically isolates the two highly energetic electrodes inside the cell. Separator breaching mechanisms culminating in internal short-circuit include:
- penetration metallic particle contaminants, generally known as burrs, of a few microns length which get into the cell during manufacture;
- sharp electrode particles penetrating a weak point in the thin separator during battery charging and discharging;
- and dendritic lithium metal that plates on the anode during charging of defective cells growing through the separator and bridging the cathode.
In an internal short circuit, current flows inside the cell and the aforementioned safety devices usually cannot prevent a thermal runaway. Figure 5 depicting the picture of a battery pack retrieved from a field failure event of a laptop computer illustrates the aftermath of what appears to be internal short-circuit of one of the six cells in an 11 V (2P/3S) battery pack built from 18650 cells. The third cell from left in Figure 5 appears to have exploded releasing all of its contents except the copper current collector.
Often only the copper current collector on the anode, due to its very high melting point (1085 °C), survives a catastrophic thermal runaway reaction from an internal short-circuit or overcharge. Thermally more stable separators based on composites of inorganic ceramics and organic polymers are being increasingly used to overcome safety hazards originating from electrode separator in Li-ion batteries.
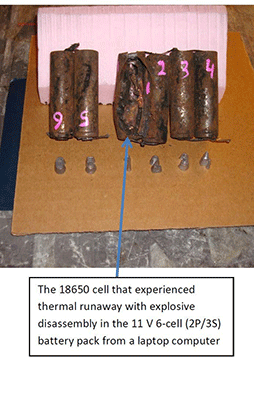
Figure 5: Depiction of the picture of a battery pack retrieved from a field failure of a laptop computer.
Building better batteries
A number of chemical and physical approaches are pursued to improve the safety of Li-ion batteries. They include the use of non-flammable electrolytes, fire retardant additives, and redox shuttle reagents (a concept initiated by this author) that lock the cell’s charge voltage at an appropriate value below the electrochemical decomposition potentials of the electrolyte and the positive electrode, and stable electrode and electrolyte materials. In commercial Li-ion battery packs, individual cell voltage cutoff limit (particularly charge voltage limit) and capacity balancing are accomplished by means of electronic circuitry. Replacing these with chemical redox shuttle reagents would increase the energy density and lower the cost of Li-ion batteries.
In conclusion, Li-ion batteries are safe when manufactured with utmost attention paid to electrode and electrolyte materials selection, design, fabrication and proper capacity matching of individual electrodes of battery cells, and optimum mechanical and electrical design enabling cells and battery packs with efficient heat management as done by many highly skilled manufactures around the world. There will always be a very low rate of failure of Li-ion batteries as in any manufactured product. Unfortunately, the safety incidents are magnified from the introduction of inferior products by unscrupulous manufactures selling them at low prices to power low-end consumer products such as hoverboards. These incidents are bringing a bad name to a widely used, enormously popular, and scientifically and commercially successful modern electrochemical energy storage device.
References
1. Gizmodo, College Kids Hope Their Hoverboards Catch Fire So They Can Finally Feel Something, http://gizmodo.com/college-kids-hope-their-hoverboards-catch-fire-so-they-1755928368
2. K. M. Abraham, The Prospects and Limits of Electrochemical Energy Storage, J. Phys. Chem. Lett., 6, 830−844 2015). http://dx.doi.org/10.1021/jz5026273
3. D. Doughty and E.P. Roth, A General Discussion of Li-ion Battery Safety, Interface, Summer 20102, pp 37.
4. D. Linden and T.B. Reddy, Handbook of Batteries, 3rd Ed. McGraw-Hill, NY 2001, chapter 35.