Electrolytic processes
The process Faraday called electrolysis — and other electrochemical research — had effects far beyond the chemist’s laboratory. New technology — electrolytic processes like electroplating and electrowinning — spurred the growth of new industries and the creating of new products.
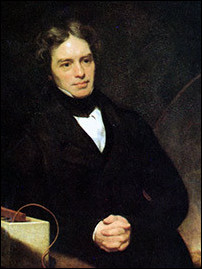
Some refer to Michael Faraday as the greatest experimentalist ever, especially because his work on electricity found expression in day-to-day technology.
Electroplating and electrowinning
Before the development of electroplating, an electrolytic technology for depositing a coating of metal, only the very wealthy could afford silver tableware. Relatively inexpensive electroplated silver eating utensils, tea services, and art objects first appeared for sale in the 1830s, providing early evidence of the usefulness of the new science of electrochemistry. This technology has since made possible the plating of many kinds of metallic films on much larger and much smaller objects then teapots — from the bumpers on luxury automobiles to computer components.
Electrowinning, the the recovery of metals from their ores partly by electrolysis, was another triumph of electrochemistry. The process was first used in the 1840s, for small amounts of gold and silver, Because early batteries could not provide large amounts of current cheaply, large-scale industrial production came only with improvements to the electromagnetic generator originally invented by Faraday. Using water power at sites like Niagara Falls to run the generators helped the industry scale up even more. the electrolytic production of aluminum and of chlorine provide two good examples of electricity’s power to separate elements from their compounds.
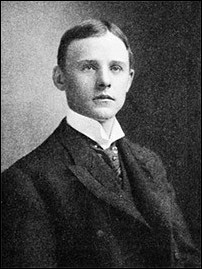
Charles Martin Hall, American inventor best known for his invention of an inexpensive method for producing aluminum.
The challenge of aluminum production
The canned beverages and foil-wrapped products that fill today’s supermarkets are evidence that aluminum is one of the most common elements in the earth’s crust. Metallic aluminum, though, was not always part of everyday life. In the nineteenth century it enjoyed the status of a semiprecious metal because natural aluminum ore was difficult to reduce to the metallic state. Although Robert Bunsen and Henri Sainte-Claire Deville managed to separate aluminum from its compounds electrolytically in 1854, they could not adapt their method for industrial use. Deville turned to producing the element by reacting aluminum chloride, one of its compounds, with sodium. Improvements in this technique then reduced the price from $4.50 to $8 per pound in 1887, but aluminum remained too expensive for everyday use.
In 1886 Charles M. Hall and Paul L. V. Héroult independently invented the electrolytic process now used for the recovery of aluminum. By dissolving aluminum oxide in fused cryolite, another aluminum compound, Hall and Hèroult were able to avoid the problems that had frustrated earlier researchers. In 1888 Hall and the metallurgist Alfred E. Hunt formed the Pittsburgh Reduction Company, now Alcoa, When this company began production, the price of a pound of aluminum fell to $2; shortly after its 1895 move to Niagara Falls, the price dropped to 75 cents and then 30 cents.
Chlorine: From brine to breakthrough products
Chlorine is another electrolytically produced chemical fundamental to much industrial production. Chlorine occurs in a wide variety of natural substances, including table salt (sodium chloride), stomach acid (hydrochloric acid), and other compounds in our blood, skin, and teeth. Its most common industrial use is to make polyvinyl chloride (PVC), the “vinyl” found in materials ranging from blood bags to siding for homes. Using electrolysis to produce chlorine from the sodium chloride in brine (salt water) also produces sodium hydroxide (alkali) and hydrogen. These chemicals are used to manufacture soaps, textiles, pharmaceuticals, plastics, and many other products.
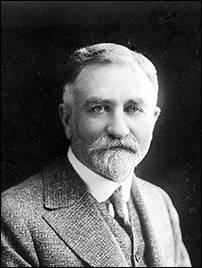
Herbert Henry Dow founded the Dow Chemical Company in 1897.
Applied electrolysis: An industrial boom
The invention in the 1890s of electrolytic cells to produce chlorine and alkali led to the founding of several of today’s large chemical companies and the expansion of others. One inventor at the time was Herbert H. Dow. Dow first developed an electrolytic process to extract bromine from Michigan brine wells; he sold the bromine to makers of medicines and photographic chemicals. He next developed a cell to produce chlorine, and on the basis of this invention, he formed The Dow Chemical Company in 1897. The company went on to extract other chemicals from brine for use in manufacturing products such as dyes and plastics. It also developed electrolytic processes to extract chemicals from seawater. Three years after Herbert Dow’s death ini 1930, the company opened its first plant to extract bromine from seawater in North Carolina. By the time of World War II, Dow plants on the Texas Gulf Coast could also extract magnesium from seawater, supplying the metal to make lightweight alloys for airplane parts.
Since the days of Herbert H. Dow, production of chlorine and alkali has changed in several important ways. Dow’s original electrolytic cells produced only chlorine, but he later installed cells with porous diaphragms that separated the chemical reactions and their products more selectively, so that usable alkali was produced at the same time. While steady improvements were made in this chlor-alkali cell design over the years, the Belgian Henri Beer in cooperation with the Italian Vittorio DeNora truly revolutionized the industry in the late 1960s. Beer and DeNora introduced electrodes made of coated titanium, which do not wear away as graphite electrodes do. This made it practical to replace earlier diaphragms with membranes made of even more elective materials, such as DuPont’s Nafion, that increased cell efficiency by preventing the passage of molecules while permitting ionis to move through.
The electric arc furnace
Another device that capitalizes on the interaction of electricity and matter, the electric arc furnace, also generated new industries to create products from its output. Unlike electrolysis, however, the electric arc furnace relies on the thermal, rather than chemical, effects of electricity to create the desired products.
Extreme heat from electricity
The French chemist Henri Moissan invented the electric arc furnace in 1892. In 1886 Moissan had already succeeded in becoming the first person to isolate fluorine, using electrolysis; he invted the furance while trying to make synthetic diamonds. In an arc furnace, an electric current crosses the gap between two carbon electrodes, giving off great heat.
Before Moissan’s time, the highest recorded temperature reached in a laboratory was around 2,000°C; he eventually made a furnace that operated at 5,000°C. Today’s arc furnaces operate at temperatures of up to 6,000°C, equivalent to that of the sun’s surface.
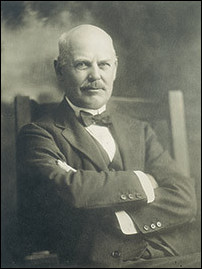
Edward Goodrich Acheson is best known for his invention of the Acheson process, which is still used to make Silicon carbide.
Central to industry
The advent of electrothermic furnaces spurred the creation of new products with many applications. In the 1890s Edward G. Acheson invented two electric-furnace products: silicon carbide (Carborundum), an abrasive used throughout industry, and artificial graphite, the pure carbon used in graphite electrodes for electric furnaces and electric batteries, and in a host of other consumer products. A tireless inventor, Acheson founded many companies, including the ancestors of Acheson Industries, UCar, and Carborundum, Inc.
Arc furnaces are central to modern industry. One third of the world’s steel is produced by this relatively clean method, and electric arcs perform the first step in separating out the silicon used in computer chips.